In the four-year ‘Art of grain-drying’ project set to commence in mid-February 2022, scientists from UNSW Sydney’s School of Chemical Engineering will work with Sanitarium’s R&D division using its pilot-scale dryer to analyse the firm’s whole wheat-grain-drying process and develop a set of protocols operators can use to optimise it.
The process is an important part of Sanitarium’s Weet-Bix manufacturing, project lead and UNSW Professor Cordelia Selomulya says.
“It’s quite a huge operation, drying tonnes of grain every day,” Prof. Selomulya explains. “The pre-cooked wheat grain comes into the dryer and has to be ‘conditioned’ to reach a certain moisture level, needed for the ‘milling, flaking and baking’ process that follows drying. As it dries, a blade is used to stir the mixture.
“Understanding the role different variables play in the drying process and how these affect grain properties is important for reducing the residence time [the time for which each batch of grain stays in the dryer], which in turn reduces the cost to the manufacturer.
“It’s also important for the design of the dryer itself. Sanitarium’s grain-dryer is working fine as it is, but we may find there’s room for improvement,” she says.
The overall objective of the project is to develop a systematic understanding of the grain-drying process from first principles of heat / mass transfer, thereby enabling better optimisation of the process, including at full scale.
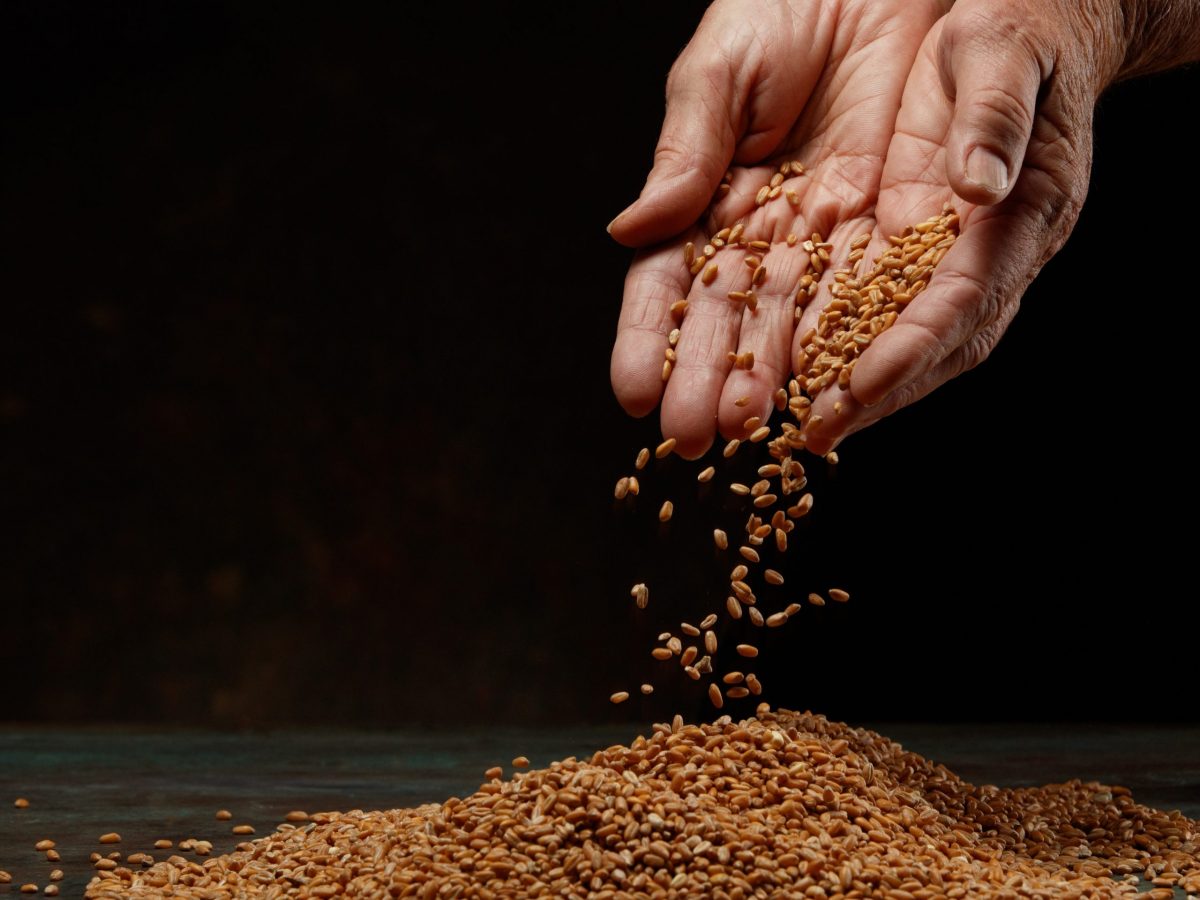
Cooked, whole-grain wheat is the basis of Sanitarium’s best-selling Weet-Bix breakfast ‘biscuits’. Credit: Shutterstock
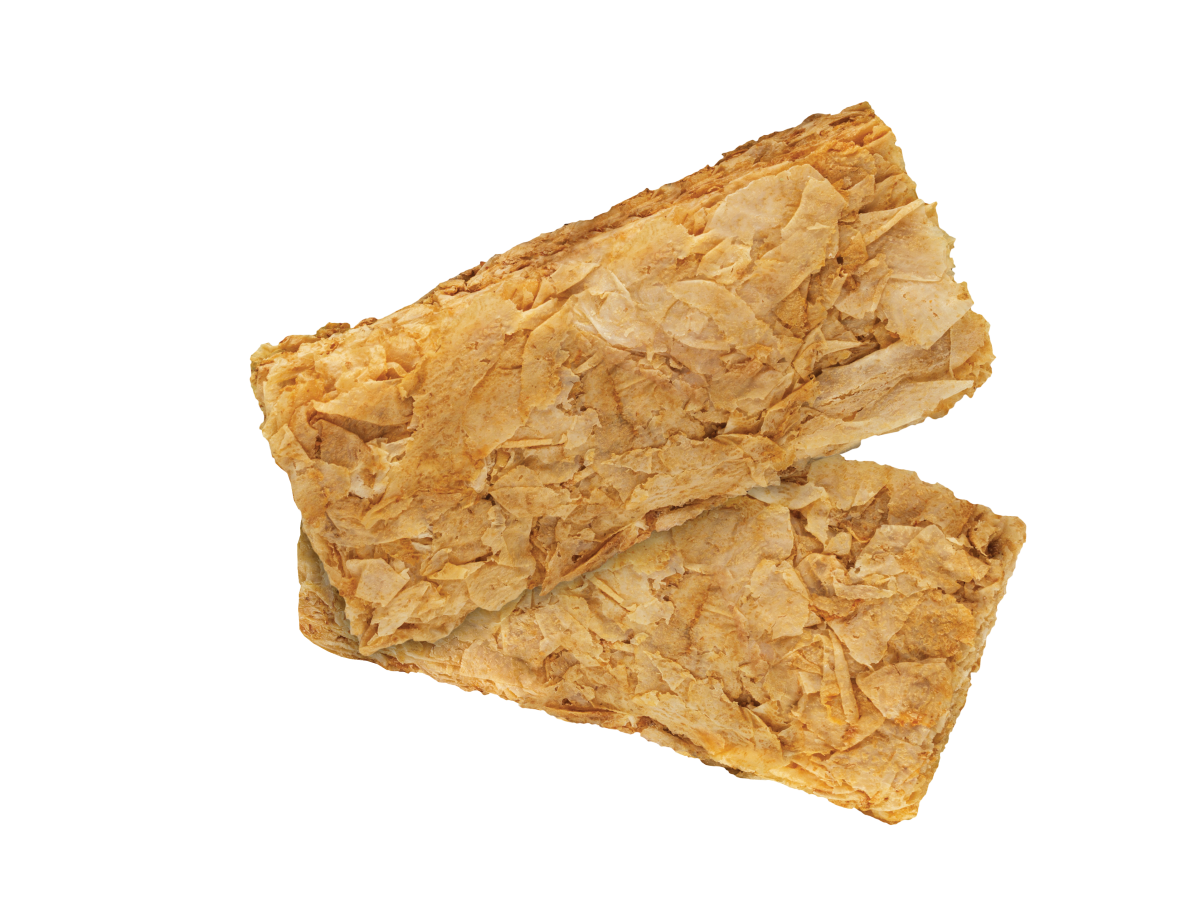
Weet-Bix out of the box. Credit Sanitarium Health Food Company
Benefits of optimising the drying process
Dr John Ashton, RMIT Professor and Strategic Research Manager for Sanitarium, says the project’s findings will help the company to streamline its grain-drying operation.
“Sanitarium’s existing grain driers were designed many years ago and do not utilise the modern sensor technology that is now available,” he explains. “By gaining an up to date understanding of the engineering science involved in the drying process, the latest engineering practice can be applied to make the grain-drying process much more efficient.
“Hopefully, it will also speed up the drying process, which is currently a limiting step in breakfast cereal manufacturing,” Professor Ashton says.
Professor Selomulya notes the economic benefits that will likely flow from the project.
“Ultimately, if Sanitarium can reduce its grain drying times, that’s money saved. And commercially, costs will be lower because you can process more grain in the same time,” Prof. Selomulya says.
The project’s findings may also have broader applications, she notes. “Essentially, the knowledge we gain through this project can be extended to other types of agricultural products, as well as to other food-manufacturing processes involving drying.”
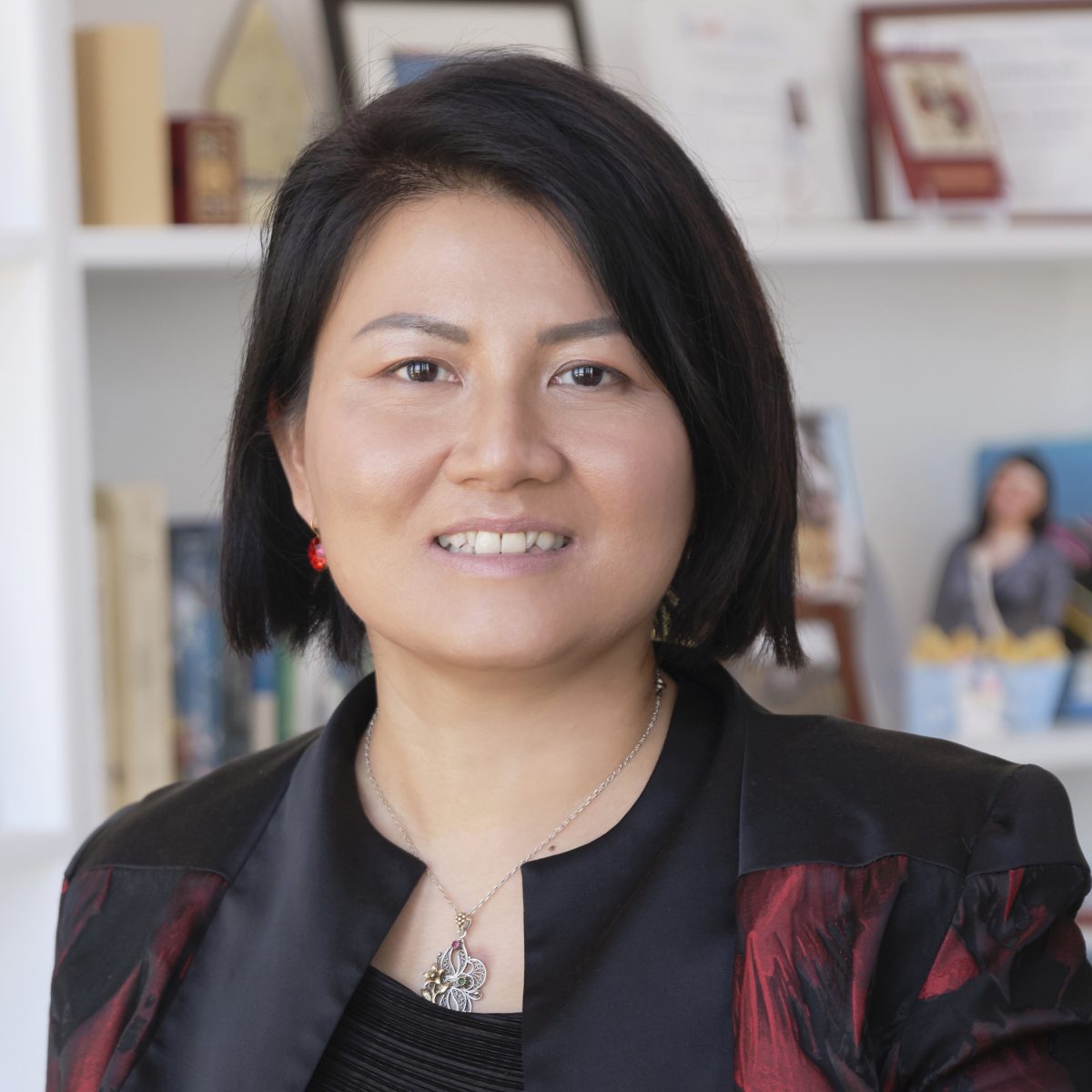
UNSW School of Chemical Engineering Professor Cordelia Selomulya will lead the four-year CRC project. Credit: UNSW
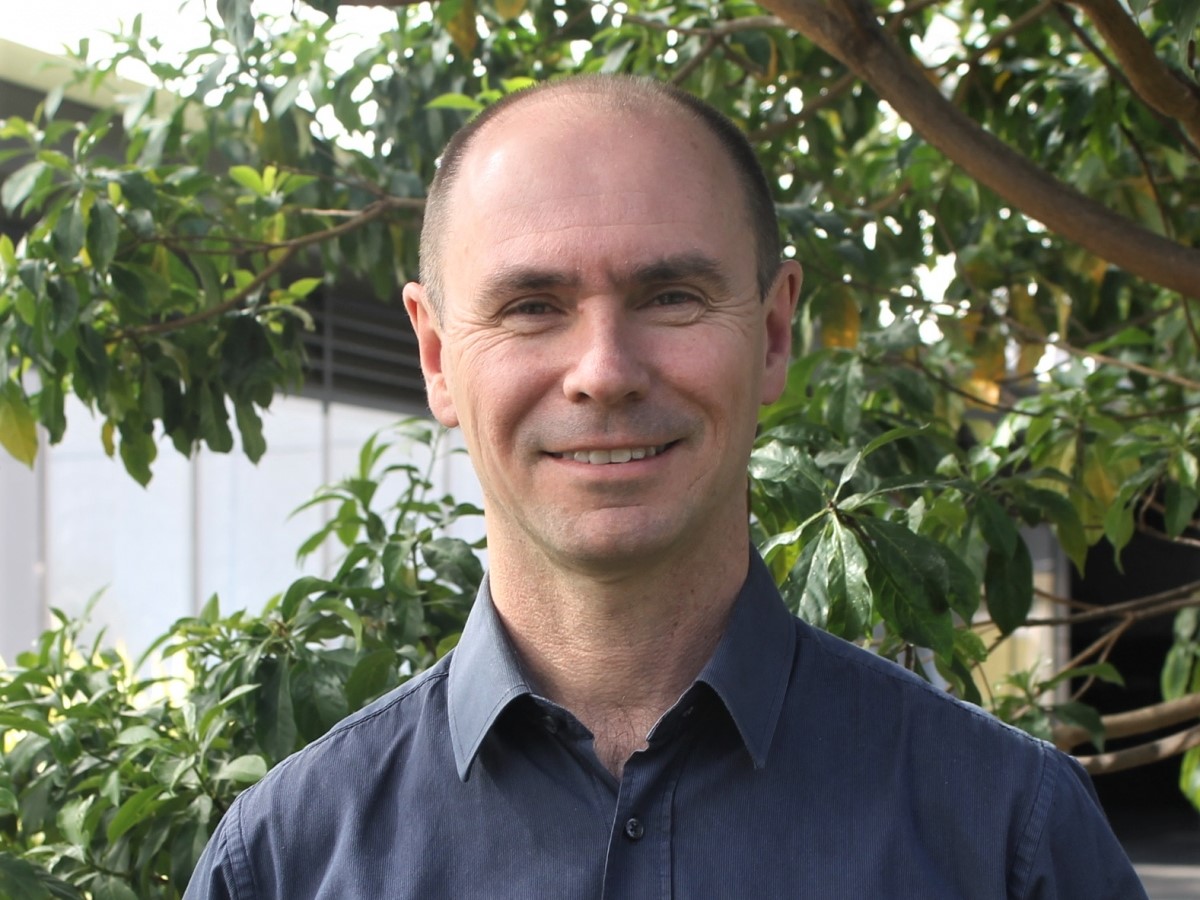
Professor Greg Leslie is the Director of UNSW’s Global Water Institute and a member of the project team. Credit: Global Water Institute/ UNSW
The project team
The four-year CRC project will be led by Professor Selomulya, from UNSW’s School of Chemical Engineering, assisted by UNSW colleague Professor Greg Leslie, Director of the Global Water Institute and the UNESCO Centre for Membrane Science and Technology.
Prof. Selomulya brings a deep understanding of the food product-drying process and of Sanitarium products to the project. Prof. Leslie is an expert in chemical engineering design with significant hands-on industry experience.
The UNSW researchers will work in close collaboration with members of Sanitarium’s R&D team.
Collectively, they’ll supervise the CRC Industry PhD student engaged on the project.
Currently, the CRC is looking for a suitable PhD candidate to join the project team. For more information, view the job ad or contact Prof. Selomulya at cordelia.selomulya@unsw.edu.au.
Lead image: The consistency and crunch of Sanitarium’s best-selling breakfast cereal, Weet-Bix, depends on perfectly dried cooked grains. “We want to optimise the drying process,” says CRC ‘Art of grain-drying’ project lead, UNSW’s Professor Cordelia Selomulya. Image credit: Sanitarium Health Food Company.